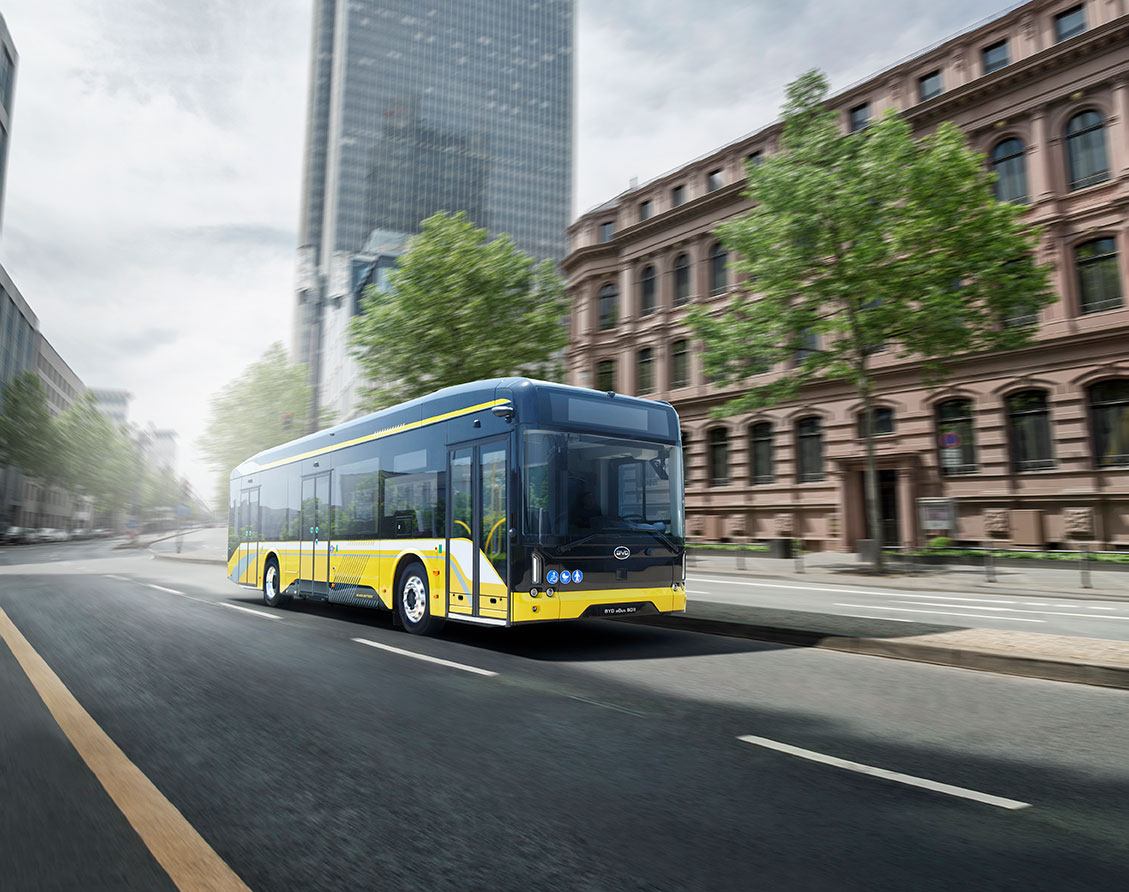
BYD to showcase its B12 eBus with Blade Battery Chassis at InnoTrans 2024
The ‘BYD eBus Blade Battery Chassis’, already seen at Busworld 2023 and ready for show at InnoTrans, to be held in Berlin on 24 - 27th October, incorporates a wave of new technologies, integrating the Lithium Iron Phosphate Blade Battery within the chassis structure, with advancements in thermal and structural safety, weight reduction and a substantial reduction in energy consumption.
BYD has chosen InnoTrans 2024 to showcase its brand new B12 platform equipped with Blade Battery Chassis. What is new, starting from here, all future BYD eBuses are set to adopt new generation Blade Battery Chassis technology with battery modules integrated in the chassis. Passenger capacity can be up to 105 people.
The group (with more than 29 years of experience in battery research and development) needs no presentation, as BYD started introducing e-buses in operation as early as in 2011 and has since evolved to become a global leader in this field with 5,100 BYD e-buses are either in operation or on order in Europe, and with more than 81,000 units of electric buses have been delivered globally, according to the OEM’s figure.

BYD Blade Battery Chassis is ready for InnoTrans
What makes BYD quite a unique case in the e-bus segment is that the group master the core technologies of the entire industrial chain, developing its own powertrain systems, power batteries, drive-motors, and motor controller system.
The ‘BYD eBus Blade Battery Chassis’, already seen at Busworld 2023 and ready for show at InnoTrans, to be held in Berlin on 24 – 27th October, integrates the Lithium Iron Phosphate Blade Battery within the chassis structure, with advancements in thermal and structural safety, weight reduction and a substantial reduction in energy consumption.
LFP Blade Batteries integrated in BYD eBus chassis
But which are the advantages brought by LFP Blade Battery integrated in the chassis? In BYD’s words, “it has passed the rigorous Nail Penetration Test and enhances the structural integrity of the vehicle. Each cell in the Blade Battery acts as a structural beam, converting steel structure weight into battery capacity, and increasing torsional stiffness to 55,000+N.m/°. Safety is also enhanced by reducing the vehicle centre of gravity by 40%, andincreasing its Tilt Angle by 47%, thus maximizing stability and manoeuvrability.
The Blade Battery is highly resistant to extreme temperatures and supports numerous charge and discharge cycles, optimizing strength and thermal stability. Also, battery space utilization is reduced by over 50% compared to traditional packs, with a higher energy density for a longer range. Overall bus weight is also reduced by 10%, increasing the range and reducing energy consumption. Its design ensures lasting efficiency, performance and a longer lifecycle”, the manufacturer states.
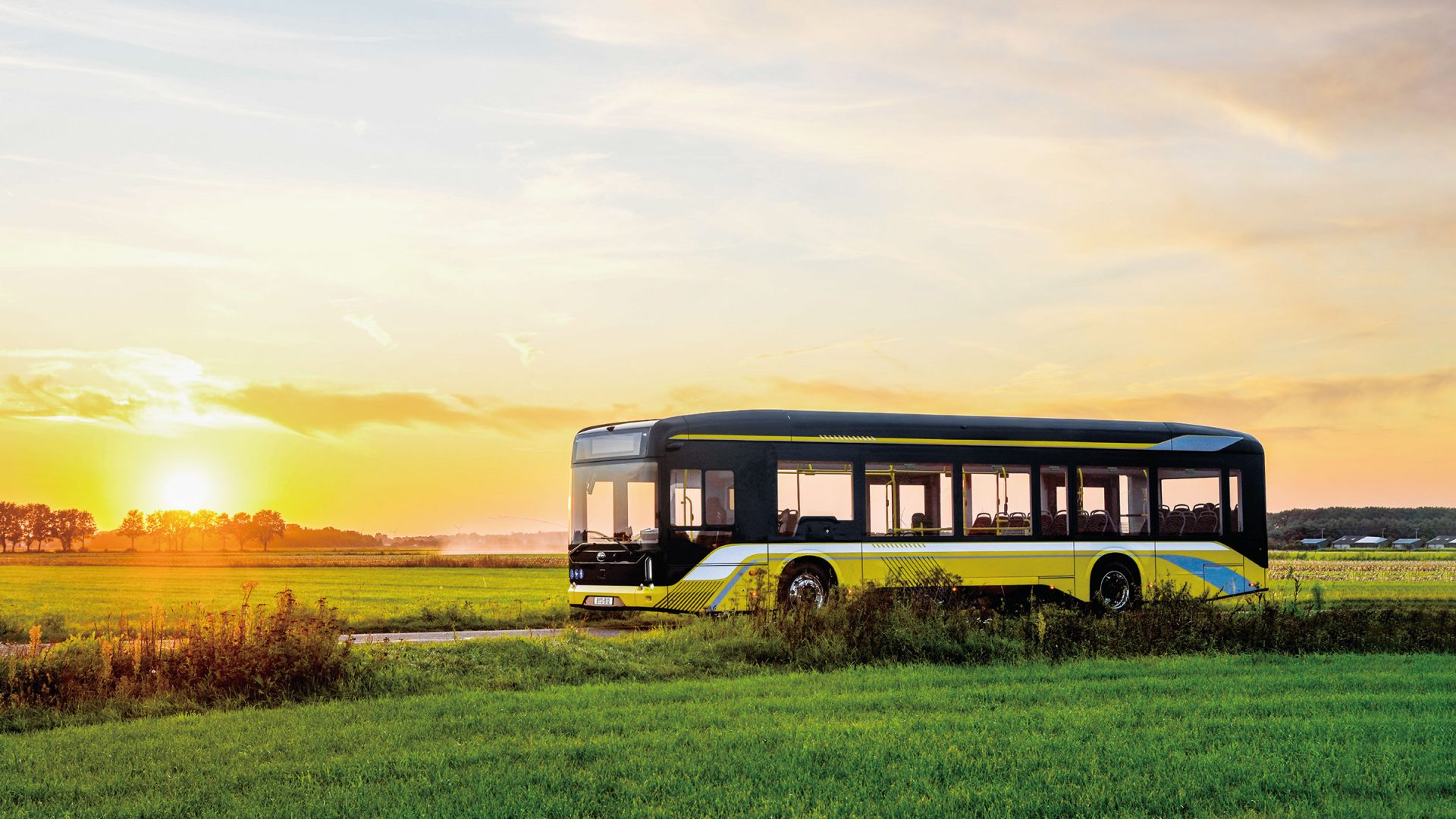
The BYD eBus Blade Battery Chassis benefits from a 6-in-1 controller with Silicon Carbide (SiC) technology, integrating 6 major electric elements in one plug and play set (drive & steering motor controllers, HV distributor, air compressor controller & DC-DC converter) for quick roadside changeover and less downtime. SiC modules are said to reduce controller weight by 15% improving vehicle efficiencies.