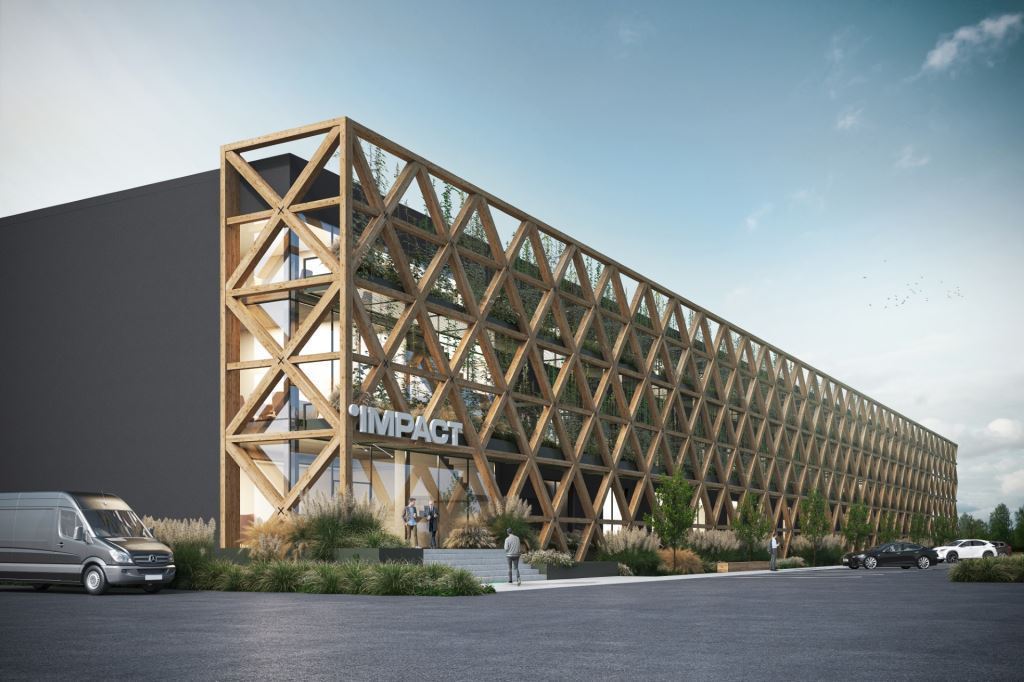
Impact Clean Designs Power Technology GigafactoryX
In a state-of-the-art factory based on Polish know-how, a battery system of up to 500 kg will be created for e-mobility and electricity generation every 11 minutes. The Polish company of Grenevia Group, Impact Clean Power Technology, shared a visualization of GigafactoryX. This is a large-scale battery factory for electric vehicles and energy storage, which will be launched in the city of Pruszków, near Warsaw.
Batteries will be made for various types of electric vehicles
The modern plant, designed in accordance with ESG issues, will be one of the largest of its kind in Europe. Its construction will increase Impact’s production capacity to 1.2 GWh in 2024 and more than 4 GWh per year in 2027. The fully automated, state-of-the-art production line will make it possible to produce a new battery for heavy duty e-mobility every 11 minutes.
GigafactoryX’s production area will eventually be 16,300 sqm. Among other things, the factory will include a battery testing facility and an advanced research and development center. Upon completion of the investment in Poland, batteries will be made for various types of electric vehicles, including those serving public transportation, such as e-buses, e-trucks and the railway sector. The plant will also produce energy storage systems designed for the commercial power industry, including for large-scale electricity storage. The battery systems will be based on lithium-ion cells in technologies: LTO (lithium titanate), LFP (iron-phosphorus) batteries and NMC (nickel-manganese) batteries.
An energy storage facility of approximately 1 MWh is also planned to work with the electricity grid
“The GigafactoryX project is another big step in the development of Impact Clean Power Technology. The first phase of the investment will allow us to increase production capacity to 1.2 GWh per year as early as next year, thanks to which we will guarantee the security of supply of battery systems for leading global brands, which are our partners. Ultimately, in 2027, production will reach 4 GWh per year. The creation of GigafactoryX means that Poland will be Europe’s leading supplier of batteries for the e-mobility industry, all based on Polish solutions” comments Bartek Kras, CEO of Impact. “Additionally, it is extremely important to us that the new plant has been designed in accordance with the principles of sustainable development” he adds.
Impact Clean Power Technologies’ business in the areas of battery systems, energy storage and electromobility is one of Grenevia Group’s four main business segments. The strong emphasis on ESG issues placed on the GigafactoryX project is a result of the Sustainability Strategy, which defines Grenevia’s commitments in this area. In the case of GigafactoryX, this includes partially powering the plant with energy from photovoltaic panels. An energy storage facility for about 1 MWh is also planned, which will work in conjunction with the photovoltaic plant and the electric grid.
It will enable the production of 16,000 battery systems
The company teamtechnik Production Technology Poland is responsible for the supply and installation of the production line that produces batteries for public transportation at GigafactoryX. It is a TDJ-owned company specializing in building automated assembly lines for the e-mobility, industrial goods and life science industries. The technologically advanced, safe production line will be dedicated to the production of battery systems for electric buses in three references, with the possibility of expanding by more.
The first phase line has dimensions of 58 by 19 meters and is thus the largest project implementation in the history of teamtechnik Poland for battery systems. Fourteen engineers worked continuously for four months on its mechanical, electrical and automation design. The flexibility of the line is influenced by the use of a production loop, which allows production to be optimized depending on the type of product being produced. As a result, it guarantees savings in both space and costs for the investor. The safety of employees operating the line is taken care of by thermal imaging cameras; when an elevated module temperature is detected, the product evacuation procedure is activated.
…………………………………………..
Podpis