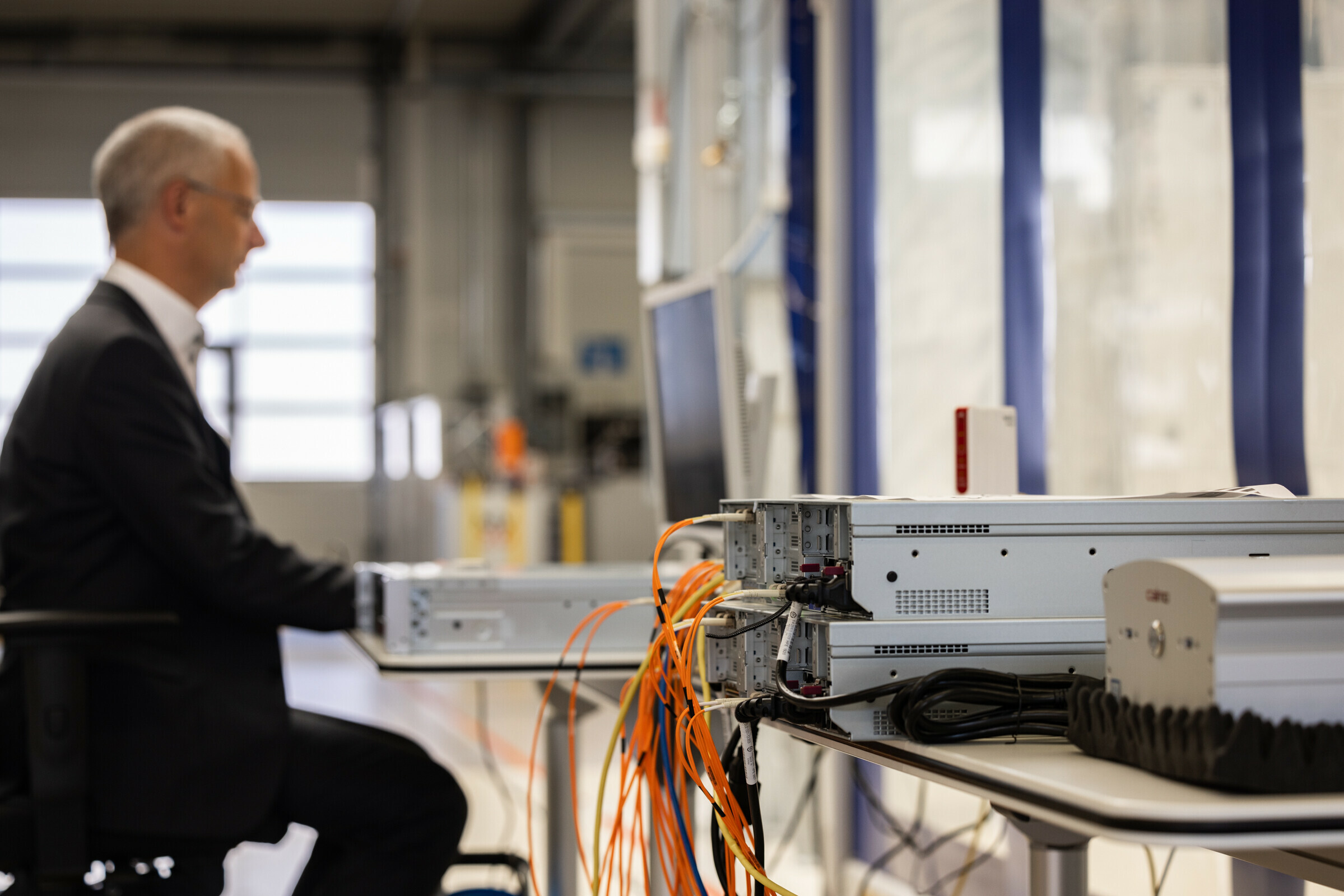
Audi Production Lab: The link between an idea and high-volume production
Audi uses its Production Lab, or P-Lab for short, to identify new and innovative technologies and reliably integrate them into production sequences. In Gaimersheim, just a few minutes drive from the Ingolstadt plant, experts under P-Lab director Henning Löser test the suitability of trailblazing new solutions for series production. That means finding and testing innovations that reliably help optimize efficiency, ergonomics, flexibility, and quality in Audi plants
Audi Production Lab: The link between an idea and high-volume production
When sharp minds work together, a comfortable couch isn’t always necessary. Certainly not in Audi’s Production Lab. Anyone who enters the hall in Gaimersheim feels like they are in a combination of a shop floor and an IT lab. In one corner are the 5G antennas. Diagonally across from them, an industrial robot is sitting on its base. Behind that are the server cabinets. IT experts sit at desks looking at their computers. “We take an idea that worked once under lab conditions and get it off the ground so it can go into stable 24/7 operation,” Löser explains. “We don’t need a big sofa or a football table for that.”
For Löser, a real production environment is much more important. In the past, new technologies were inadequately assessed because Audi couldn’t try them out first. To change that, the company with the four rings created the Production Lab in 2012. Since then, Henning Löser’s team has tested intelligent assistance systems that employees support with new variants in the mesh between the person and the machine. These systems conserve resources and continuously develop and improve procedural safety and workplace ergonomics. One example is modular assembly, Audi’s assembly and logistics concept that is the only one of its kind in the world.
Every day, experts research and test new high-tech solutions like Ingolstadt shop floor IT or 5G for mass production suitability in increasingly networked, digitalized production. “In the process, we are constantly in touch with our colleagues in production so we can be sure we can implement our ideas,” says Löser, who has overseen the P-Lab since 2016. “We show them exactly what we’re working on. There’s no point in us developing something theoretical that nobody uses in practice. We test and learn.”
Stability Is Critical
Stable production is critical for Audi and the P-Lab. “Our goal is 99.9 percent reliability,” says Löser. “We must assess how good uptime is in daily use.” How good is the corresponding service concept? How should colleagues from maintenance be trained so that the new application operates without interruption? “We only transfer new technology into production when our colleagues say something truly helps them,” the P-Lab boss explains. Another important factor is whether a good area of application even exists within the production process.
Paradigm Shift in Automation
The technologies that have occupied the workers in the P-Lab over the past ten years have changed significantly. They operate on the principle of ‘higher, faster, further’. “Making production better is like a competitive sport,” says Löser. “That means we use more cameras, more sensors, and above all, more algorithms in production.” Nonetheless, the system must operate steadily. “Make things as simple as possible. Then they won’t break,” the P-Lab boss says.
Right now, a paradigm shift in automation is well underway. “If we use 100,000 cameras in production, we also have 100,000 industrial PCs that do the assessment,” he explains. “But then who takes care of maintenance and repairs on that equipment? Who updates the operating systems? At some point, the cost of maintenance exploded.” Driverless vehicles are another example. The more Audi uses, the more functionality and fleet managers it needs.
On top of that, there is also equipment maintenance and monitoring. “The overall efficiency has to be right,” says Löser. The solution: work based on software and cloud technology. Updates go via the server – with three mouse clicks. Löser says, “Right now, we’re running our shop floor IT in the Ingolstadt Heifer via a central server solution.”
Experts Are Looking Toward the Future
The P-Lab plans and tests far in advance. According to Löser, traditional production planning did not allow that kind of leeway. 5G is one example. Since 2018, the P-Lab in Gaimersheim has operated a 5G base station. To use 5G as a radio network suitable for automated production, the standards that must be applied are not the same as those for downloading videos. For example, controlling the equipment requires URLLC (Ultra-Reliable Low-Latency Communications). The tests in Gaimersheim enabled them to work out requirements for the global 3GPP standard and contribute them to groups that maintain standards. “We did our part to make 5G function seamlessly as a radio standard in automation,” Löser explains. The lab’s work ranges from controls for a safety cell with robots that must turn everything off within ten milliseconds to logistics applications that link containers using massive device connectivity. “We’ll need that when it comes to the future of production and logistics,” says Löser.
Direct Exchange Makes Pragmatic Solutions Possible
Today, more than 30 staff members from the Production Lab work closely with the various sites. Because inter-departmental colleagues from all production areas work simultaneously in the P-Lab on a range of projects, the number of workers is multiplied five or six times by temporary lab users. “Something is always going on in the P-Lab. Direct interaction with the users is important,” says Löser. Audi Production thrives on an open innovation culture, enabling the team to innovate. It makes the P-Lab an attractive employer for ambitious IT experts and engineers.
Löser says that technologies can drift to a certain point in a lab. The most recent mistakes only arise through use and must be eliminated on the spot. “To stay flexible, we need a smart factory that responds quickly to fluctuations in demand,” says Löser. “We can’t just try out new ideas in serial production while it’s happening. That would be disastrous. We’re in the P-Lab to do the necessary tests and take the next steps in smaller pilot projects. After that, we test out the technology, for instance, in the real lab of the Ingolstadt Heifer and take it to mass production from there.“