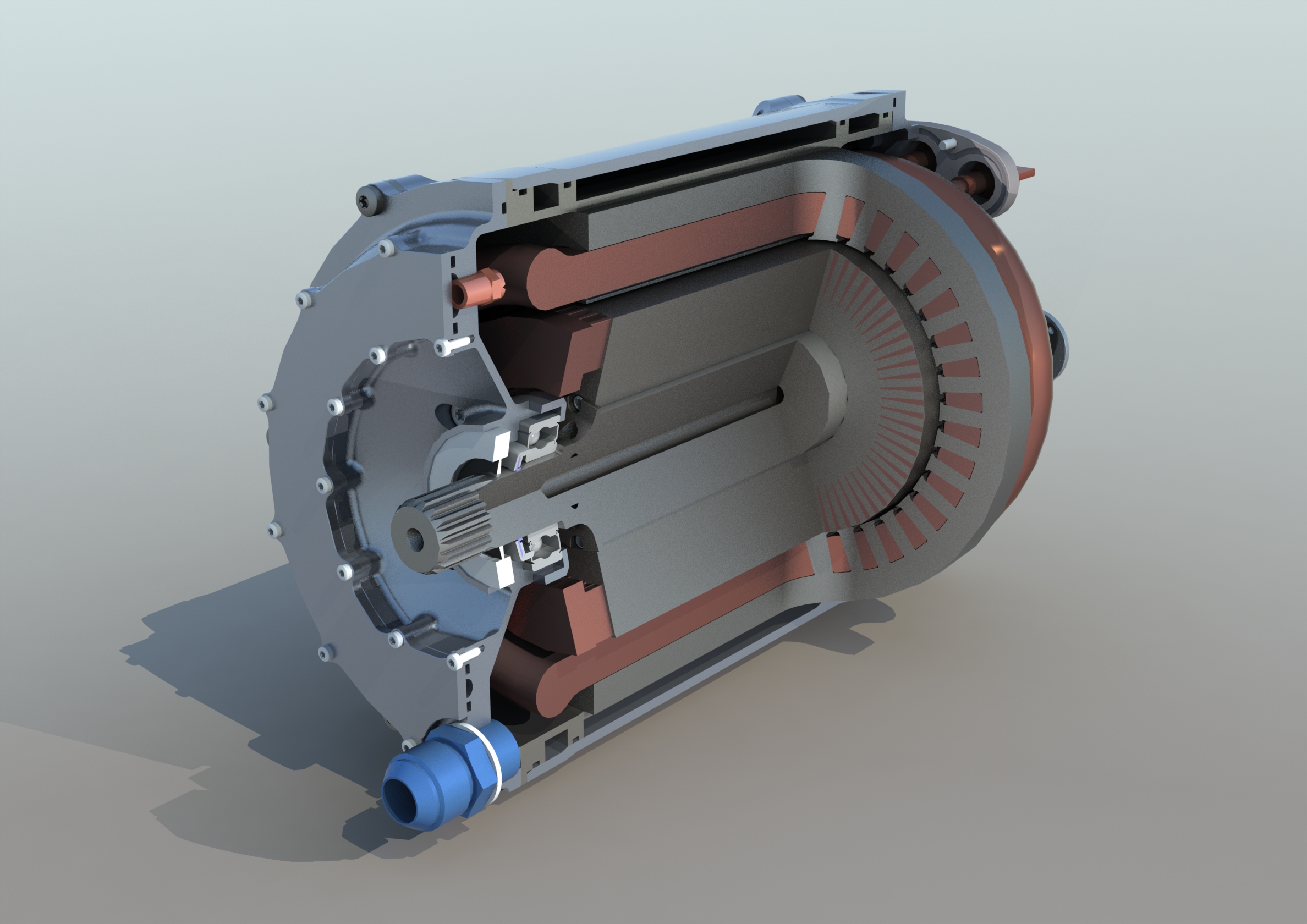
DSD TO CHALLENGE THE ACCEPTED DOMINANCE OF PERMANENT MAGNET MACHINES FOR EV PROPULSION
Presentation at The Battery Show and EV Tech Digital Days will show surprising outcome from fundamental study
Leading electrified powertrain engineering consultancy, Drive System Design (DSD), will challenge accepted views on motor topology at The Battery Show & EV Tech Digital Days, a virtual conference and expo scheduled for November 10th-12th. Paul Sims, Chief Technical Specialist, DSD, will present an in-depth study showing that, under certain conditions, an induction machine can be superior to its permanent magnet equivalent.
Interest in an alternative to permanent magnet topology for e-machines stems from pressure on the supply of rare earth magnets as demand grows. Rare earth materials are central to achieving high power density but rapidly growing demand is causing raw material price fluctuations that can completely erode typical automotive profit margins.
The accepted view is that permanent magnet machines are more efficient and more power dense than induction machines but the DSD study has revealed that for some vehicle types, the operating points and durations in their typical drive cycle result in the induction machine operating in its higher efficiency regions more often than a permanent magnet machine. Counter-intuitively, despite the permanent magnet machine’s advantage in peak efficiency, the overall energy required to complete such a drive cycle can be lower with an induction machine.
Sims’ paper, entitled Induction Machines for Electric Drive Systems – Reducing Reliance on Rare Earth Magnets, will detail the work carried out to successfully achieve a high specific output from an induction machine that supports its use as a primary traction device. It summarises the technical challenges faced and explains the potential energy benefit of induction machine topology when applied to traction systems.
One of the key elements in DSD’s approach was the use of its in-house concept architecture selection tool, ePOP (electrified Powetrain Optimisation Process) to allow unprecedented insight into multiple powertrain configurations, potential trade-offs and areas needing development. This tool indicated that high specific performance induction machines have the potential to achieve the required vehicle performance and efficiency targets. The challenge then becomes achieving the required performance through techniques such as engineering adequate rotor integrity at high rotation speeds and maximizing thermal management techniques.